Robotic arm fiber laser welding machine adopts advanced fiber laser to output laser beam with high energy and density, which will shine on the metal surface after focusing, so that the workpiece will be vaporized or melted at the moment of being irradiated by the ultra-fine focus, so as to achieve the welding effect. Automatic welding or cutting can be achieved by programming a CNC mechanical system to move the spot irradiation position. Its main advantage is that it can automatically track and locate the weld seam based on the product, and can achieve functions such as weld seam inspection, weld seam tracking, scanning before welding, and adaptive arc tracking.
Equipment characteristics
1.Adopts the six axis linkage of the manipulator to carry out 3D precision welding of 3D hardware parts. The non-contact weld seam tracking system and multi station coordinated work can realize intelligent and automatic production, save time and labor, and reduce production costs in an all-round way.
2. With high positioning accuracy and a wide processing range, the robot arm is controlled by a handheld terminal to enter the warehouse. The overall structure is compact, and efficient operation can still be achieved even in places with harsh conditions and many restrictions
Applcation area:
Widely used in industries such as automobiles, heavy industry machinery, aerospace, electrical appliances, hardware, 3C electronic components, etc. Help enterprises save labor, improve product quality and production efficiency, and become the new generation of laser equipment for artificial intelligence.
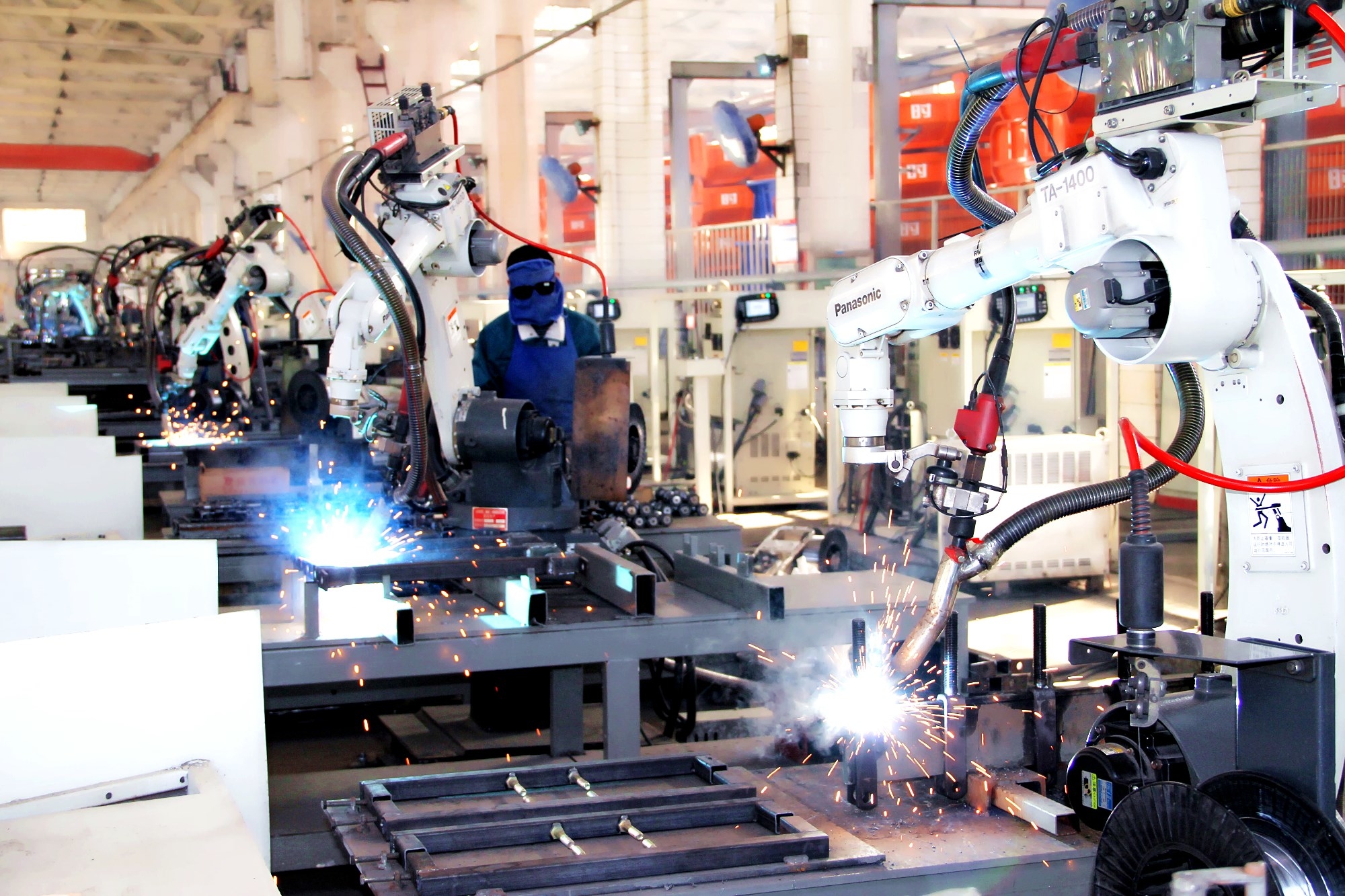
Laser welding robot
Industrial robot | DC-SC2000 | |
---|---|---|
Degree of freedom | 6 | |
specified load | 20Kg | |
Maximum working radius | 1848mm | |
Repeatability | ±0.06mm | |
Range of motion | J1 | ±160° |
J2 | -175°/+75° | |
J3 | +40°/ +265° | |
J4 | ±180° | |
J5 | ±125° | |
J6 | ±360° | |
Rated speed | J1 | 99°/s,1.73rad/s |
J2 | 87°/s,1.52rad/s | |
J3 | 144°/s,2.51rad/s | |
J4 | 180°/s,3.14rad/s | |
J5 | 180°/s,3.14rad/s | |
J6 | 225°/s,3.92rad/s | |
Maximum speed | J1 | 148°/s,2.59rad/s |
J2 | 109°/s,1.9rad/s | |
J3 | 172°/s,3.01rad/s | |
J4 | 300°/s,5.23rad/s | |
J5 | 300°/s,5.23rad/s | |
J6 | 375°/s,6.54rad/s | |
Allowable moment of inertia | J6 | 0.8kg㎡ |
J5 | 3.3kg㎡ | |
J4 | 8.7kg㎡ | |
Allowable torque | J6 | 30.7Nm |
J5 | 73.4Nm | |
J4 | 140.4Nm | |
Applicable environment | temperature | 0~45° |
humidity | 20%~80% | |
other | Avoid contact with flammable, explosive or corrosive gases and liquids. Keep away from electronic noise sources (plasma). | |
Cable Length of Instructor | 8metre | |
Body-cabinet connection length | 6metre | |
I/Oparameter | Digital:32 inputs, 31 outputs (one for control cabinet fault indicator output) | |
battery capacity | 5.6kVA | |
rated power | 4.5kW | |
Rated voltage | Three phaseAC380V | |
Rated current | 8.1A | |
Body protection grade | IP54 | |
Installation method | Ground installation, upside down installation | |
Body weight | 305kg | |
Control cabinet protection grade | IP53 | |
Control cabinet size | 750mm(wide)×486mm(thick)×1030mm(high)-立式 | |
Control cabinet weight | 186kg |